AP Diving’s dedicated R&D facility in Helston, Cornwall, UK
Many people ask us why we build things the way we do. Maybe if we outsourced more and obsessed less about safety and performance, we’d be as cheap as our competitors, quality would still be good enough and most divers wouldn’t notice the difference?
We say: ‘Good enough’ never is. And 'most divers' deserve a bit more respect.
The same spirit that motivates great divers to explore uncharted territory drives us to push the limits of what dive equipment can do. Over the past 20 years we’ve employed specialist product designers and invested heavily in advanced test facilities to stay at the top of our game so you can perfect yours.
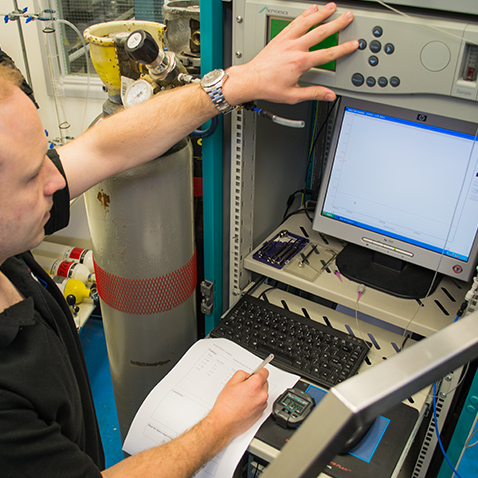
It’s an approach that’s won numerous awards, dozens of patents and helped 1000s of divers around the world beat their own personal diving goals.
When you buy AP Diving equipment, you’re investing in gear that’s been fine-tuned by years of R&D, quality control and punishing test regimes. It’ll serve you well every dive for years to come.

THE WORLD’S LEADING COMMERCIAL REBREATHER TEST CENTRE
Our on-site R&D centre houses two of the world’s most advanced ANSTI test systems - a 200m Breathing Simulator and the R&D Demand Regulator Test Facility. These are fully integrated lab systems designed specifically to measure the dynamic breathing performance of our rebreathers and components to stringent European Standards: EN250:2000 and EN14143: 2003. Together, they allow us to work breathing apparatus hard, at depth, in water temperatures from -4°C to +50°C.
Because this full test regime lies behind everything we make, you’re guaranteed:
- Low work of breathing even at depth
- Optimum counterlung placement – for both front & back-mounted options - ensuring excellent breathing characteristics in all diving positions
- Canister performance based on real tests in harsh conditions, not on the surface but deep down - where it counts
SHARE THE KNOWLEDGE
Our extensive research ability benefits the knowledge-base of the rebreather diving community as a whole. We are at the forefront of establishing best practice for all aspects of rebreather diving from choice of scrubber material, to counterlung design and placement, scrubber-life and CO2 monitoring to evaluating oxygen cell performance.
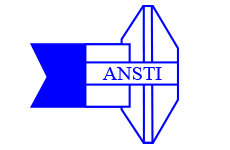
WHAT IS ANSTI?
ANSTI Test Systems Ltd design and manufacture test facilities to measure the performance of underwater breathing apparatus. They use computerised data acquisition techniques to display in real-time the dynamic performance of breathing apparatus under test.

THE ANSTI 200M BREATHING SIMULATOR
Rebreather Test Facility
Commissioned in 2004, the ANSTI 200m Breathing Simulator was the first ever system built on this scale and was custom made specifically to meet our rebreather R&D programme. The test vessel is large enough to accommodate all models in the Inspiration range in the main swim and head upright positions and in any attitude of pitch and roll.
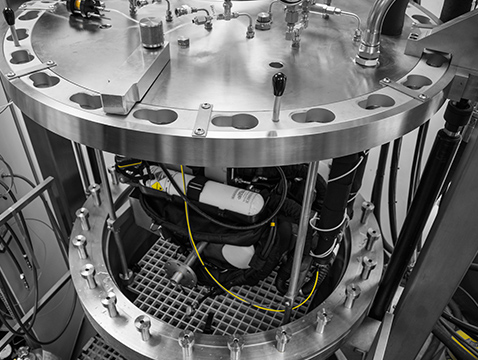
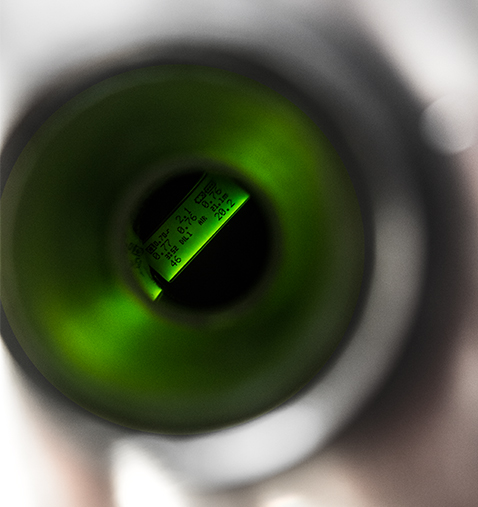
Dive Simulation
We simulate dives in all conditions - breathing rates, water temperatures and depths down to 200m. As an in-house facility, we are can repeat tests indefinitely, uninhibited by the time, logistics and cost restrictions of using an external test house. This means we’re continually refining data, and discovering new things about rebreather performance, such as:
- Work of Breathing ratings with different breathing mixtures at different depths
- PO2 Setpoint control accuracy
- Endurance, reliability and accuracy trials
- CO2 Scrubber endurance (across the range of depths & conditions)
- Scrubber Temp-Stick trials
- Various brand Scrubber material comparison tests
- Hydrostatic imbalance trials to ensure that the Counter-lungs are located in the ideal position to achieve optimum breathing performance in all attitudes of pitch or roll.
More information = better products = a better diving experience
All of this collated data, in particular the CO2 Scrubber Endurance trials - conducted across the full spectrum of influence, CO2 production rates, breathing rates, water temperatures and depths - and the ability to systematically comparative-test the various brands and types of scrubber material on the market, is information that can benefit both ourselves as manufacturers but also ultimately, the knowledge-base of the rebreather diving community as a whole.
Mouthpiece testing
The system features a specially designed Sheffield (anatomically correct) head with adapters to connect and test other life support elements such as the full-face masks and OC/CC switch mouthpieces. Measuring CO2 breath by breath we can discover and then eliminate any ‘dead-space’ (i.e. areas where CO2 may accumulate). This test capability is absolutely crucial to developing a product from concept to prototype then fine-tuning before launch.
Advanced safety & accuracy
Unique among rebreather manufacturers, we can simulate super fast descents and ascents under various conditions. The ultimate performance challenge for any closed circuit rebreather is a hard-breathing fast ascent. All Inspiration models are put through this test to ensure design integrity.
The Stainless Steel Breathing simulator is fitted with a pure sine wave drive linkage. It has variable tidal volume and push button control of breathing rate. The breathing system is fitted with a heating and humidification system which, together with a hyper-efficient temperature control system allows us to perform test dives from -4C to +50C exceeding the test requirements of BS EN250: 2000
The scrubber test system uses a mass flow controller to inject, at all depths, a calibrated flow of carbon dioxide into the breathing circuit simulating the full range of diver work-rates.

THE ANSTI REGULATOR
TEST FACILITY
Quality Control and R&D
The first of its type ever built by ANSTI, this facility tests the performance of smaller products such as the Auto Air octo-inflator, the rebreather First Stages, the ADV - Auto Diluent Valve - and many new products under development. It also performs routine but essential Quality Control and QA procedures across our product range.
Rated to a maximum depth of 80msw, the computer and instrumentation system records the test depth and real-time response of high pressure, inter-stage pressure, mouthpiece differential pressure and stroke.
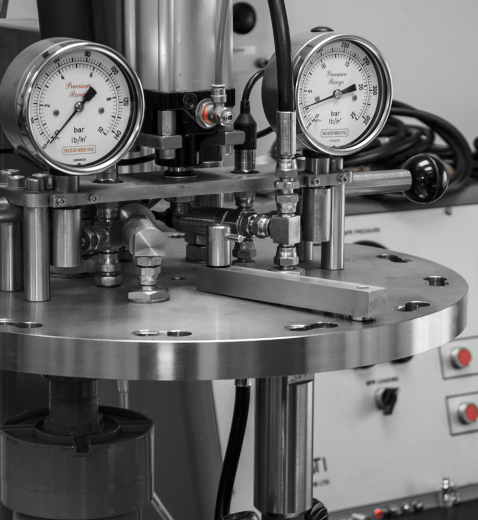

THE FUTURE?
We are discovering vast improvements to rebreather performance, inventing solutions to issues that other companies haven’t even realised are the key to the future. We’ll keep investing in the research technology needed to progress the science and advance the frontiers of what’s achievable in diving. Because if it’s do-able, we want to do it.
Exciting (and testing) times ahead….